At Foodmach, we’re making a pledge to do everything possible to achieve carbon neutrality as quickly as possible.
We believe we have a responsibility to ourselves, our customers and our entire supply chain to decarbonise quickly, without passing costs along.
This requires complete business transformation and puts safety—of people, the planet and our business ecosystem—at the heart of everything we do.
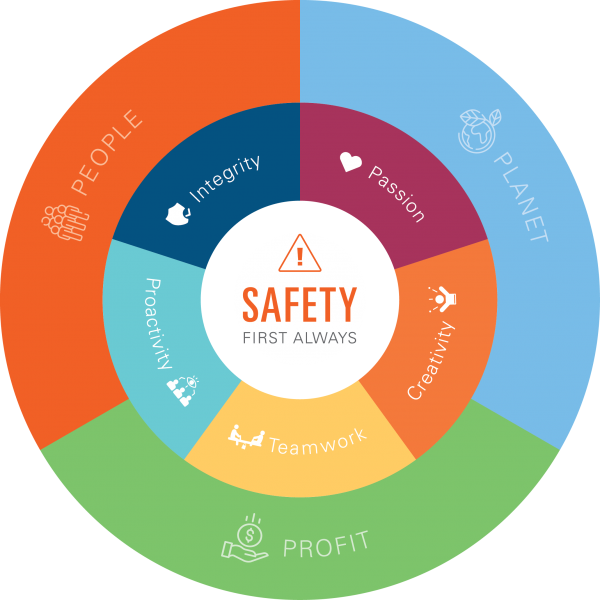
We also believe that simply using carbon offsets does not solve the real problem.
We’re prepared to do the hard but more meaningful and permanent work to reduce our own carbon emissions.
And we’re committing to transparency around our actual emissions reductions versus our offsets.
Equally critical is the work we’re doing to help our customers reduce waste and decarbonise their packaging lines.
We're achieving this through energy-efficient technology, Industry 4.0 integration and the packaging industry’s most sophisticated (yet intuitive) line control systems.
What we’ve done so far
- We’ve developed ESG Programs and a Sustainability Policy
- We’re embedding them into our culture, systems, processes and procedures.
- Our factory in Victoria runs on 100% renewable energy
In 2013, we installed a 400-panel solar system that generates almost 50% of our energy requirements, and we changed much of our lighting to LED.
This year, we’ve appointed Momentum Energy to be our renewable energy supplier. We pay an additional fee per kWh for electricity supplied to our factory for GreenPower. GreenPower is a government-accredited renewable energy product offered by most electricity retailers to households and businesses in Australia.
Although we consume power from the grid, which can be generated from many different sources, the fee that we pay Momentum means that they will ensure that power from GreenPower accredited sources is generated and exported to the grid to match our usage.
- We’ve boosted our energy efficiency
We’ve completed changing all the lighting in our 5,500m2 factory to LED, resulting in energy savings for lighting of around 30%.
We’re investing in energy-efficient equipment, for example, our new 4kW Fibre Optic Laser Cutter which replaced an older laser. The new machine uses significantly less energy and assisted gases (nitrogen and oxygen) and cuts faster with less heat.
- We’ve reduced waste at all levels
We’ve implemented a stringent and transformative process of Lean Manufacturing, Continual Improvement and digitalisation within the business, which is ongoing and has significantly reduced waste throughout our entire value chain.
- We’ve developed products to help our customers decarbonise.
A decade of research and development has gone into Line MES, a line control software packaging that contributes to overall sustainability efforts by reducing waste at every stage of the packaging process, be it time, energy, materials or human resources.
Line MES supports traceability initiatives and is a foundation for the transition to full Industry 4.0.
- Rapid, automated recipe-driven changeovers and optionally, automatic sourcing of materials.
- Automated line optimisation, where machine learning algorithms using standardised data in real-time to automatically make adjustments for OEE.
- End-to-end integrated quality control monitoring.
- True OEE (Overall Equipment Effectiveness), not partial. Reasons for downtime and stoppages, underperforming equipment and under-optimised production runs are made completely transparent, eliminating opportunities for operators to exert influence over delay accounting.
Although most beneficial for high-speed lines running an extensive range of SKUs, Line MES is a resource-saver and production-optimiser for any speed line.
That's why it's award-winning.
What we’re working on now
- Putting our transformation to a Net Zero and True Zero business at the heart of our business strategy and product and service innovation.
- Implementing behavioural strategies for our team members to understand the impacts of every decision we make and action we take.
- Looking for further opportunities to work with our suppliers to decarbonise our supply chain.
- For our customers, we’re designing automation that helps them reduce their reliance on non-sustainable packaging materials. We’re promoting internal R&D and partnerships with the science community to accelerate the pace of discovery, scaling and adoption of new innovations to minimise the carbon footprint of packaging automation (and, therefore packaging).
- Collaborating with OEM suppliers of componentry to identify ways to make our equipment more energy efficient so we can offer our customers options to support their carbon reduction strategies.
We already use variable speed drives to reduce power consumption on some of our products.
We’re working with our pneumatics supplier to modify the design of our key product ranges to use less air.
What we’ve got planned for the near future
- Work with a consulting agency to assess our total emissions and carbon footprint, following protocols toward science-based targets.
- Follow a carbon-neutral framework and embed Environmental Management Systems into our business.
- To look not just at CO2 reductions but to also consider methane (CH₄) and nitrous oxide (N2O), which have 30 and 300 times the heat-trapping effect of carbon dioxide, respectively. Also, hydrofluorocarbons (HFC), which can have a relative climate impact that is hundreds to thousands of times greater than CO2.
- Reducing and/or offsetting non-power-related emissions from company activities, such as business travel.
In the longer term
- Reduce emissions along the supply chain in the development and manufacture of our products.
- Actively work towards providing our customers with Net Zero packaging machinery.
- Work with our industry partners and organisations to transition the industry as a whole further towards environmental sustainability.
The World Economic Forum has stated that the world has no chance of reaching Net Zero unless clean energy investments in developing countries are supported.
70% of funding will need to come from the private sector.
So we also pledge to work along our international supply chain and with investment companies to support these efforts.
Net Zero provides a goal but not a path to achieving it.
The business environment is complex and interdependent, machinery manufacture and supply even more so.
Without stronger national and international policies and enforcement and a coordinated global transition plan, what we’re intending to do is momentous.
But we’ll find a way because we have to.
That’s our commitment to the future.
Just ask us
See our ESG Programs
Back to About Page